The Process of Injection Molding
The injection molding process is a manufacturing method that injects melted plastic into an intricately designed mold to create precise, high-quality parts in large volumes.
It is the heart of modern manufacturing. Think about how many plastic components contribute to our daily lives… (Try counting each plastic piece on your car dashboard for perspective)
It’s a process that shapes everything from the smallest components to large industrial parts with precision and efficiency. Injection molding companies have become essential across industries like automotive, electronics, and consumer goods.
As we continue to fly through 2024, it is clear that keeping ahead of the curve in injection molding is necessary for staying competitive in the manufacturing world.
Diagram: Injection Molding Process Step by Step
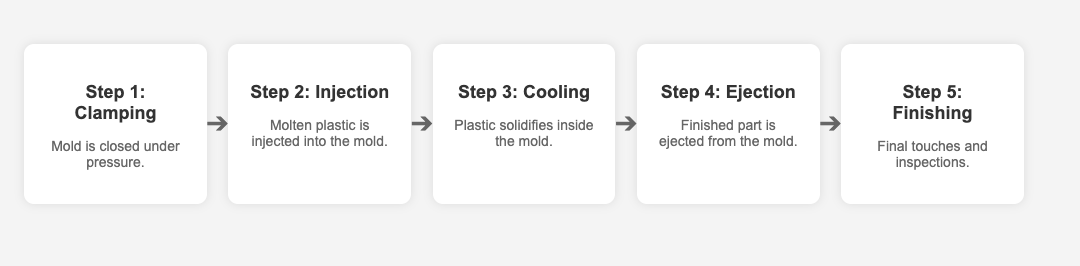
What is Injection Molding?
The big picture is easy to grasp. Most of us have seen what happens to heated plastic - it becomes liquid and moldable before it cools and hardens.
The science lies in the details. Mold design, material selection, quality control, rapid prototyping with adjustments, this is where expertise and wider capabilities come into play.
A well-designed and expertly-run injection molding facility can do all this and more.
The injection molding process is known for producing large quantities of identical parts with high accuracy and minimal waste. Injection molding is central to manufacturing because it offers:
Key Takeaways:
- High efficiency for mass production.
- Flexibility in design.
- Consistency in product quality.
- Cost-effectiveness for large volumes.
- Use across various industries (automotive, electronics, etc.).
Components of the Injection Molding Machine
Injection Unit
The injection unit is the workhorse of the injection molding machine. It takes plastic pellets from the hopper, melts them in the barrel, and then pushes the molten plastic through a screw into the mold.
The precision and control in this process ensure that each part meets exact specifications. Without this step, the process wouldn’t have the consistency or accuracy needed for high-quality production.
Clamping Unit
The clamping unit holds the mold closed during the injection and cooling stages.
This unit applies immense force to keep the mold halves together, preventing any material from leaking out. The exact pressure applied is important to ensure the final product’s dimensions and quality are spot on. The entire process could fail without precise clamping.
Mold
The mold is the heart of the process. It is where molten plastic takes shape.
It consists of two halves - the cavity and the core - which come together to form the shape of the part.
Common mold materials are steel and aluminum. They offer different benefits depending on the needs of the project. Each material choice impacts the production speed, cost, and durability of the mold.
Comparison of Mold Materials
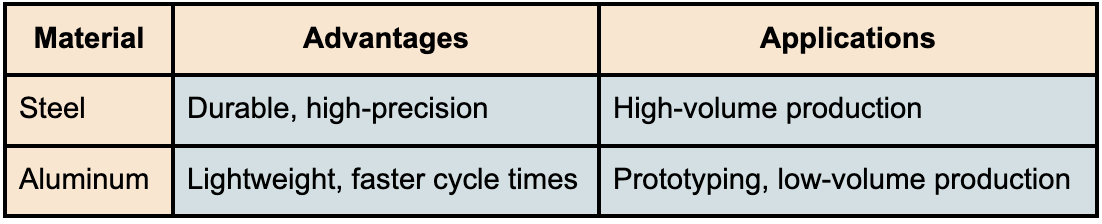
The Injection Molding Cycle
Step 1: Clamping
Clamping is the first step in the injection molding process.
The mold is securely clamped shut by applying significant force to prevent any material from escaping during injection.
This clamping force is critical because it maintains the mold's alignment and creates a sealed cavity where it injects the plastic. The strength of the clamping unit is matched to the size and complexity of the desired part.
Step 2: Injection
In the injection phase, thermoplastic material melts inside the unit and injects into the mold using a pressurized screw.
This step directly impacts the final product's quality by achieving exact specifications. As the mold fills, the plastic cools and solidifies to stabilize the shape and prevent warping or dimensional issues.
Step 3: Dwelling and Cooling
The dwelling phase begins after the molten plastic fills the mold.
The plastic is held under pressure to compensate for any material shrinkage as it cools. This pressure, known as packing pressure, forces additional material into the mold to fill any gaps left by shrinking.
This step is vital in preventing surface defects and ensuring that the part has the desired density and strength.
Following the dwelling phase, the cooling process solidifies the plastic inside the mold.
Cooling time varies depending on the material used and the thickness of the part. Plastic cooling too quickly or unevenly can lead to warping, internal stresses, or incomplete filling.
Step 4: Ejection
The final stage of the injection molding process is injection! At this point, the material has cooled and taken its desired shape.
Ejector pins push the part out of the open mold cavity.
This step must be executed with precision to avoid damaging the part. Ejecting the part too forcefully can cause cracks or deformities, while insufficient ejection force might leave the part stuck in the mold.
The part may undergo further processing after injection. The manufacturer may need to trim or inspect it before it’s ready for use.
Common Thermoplastics Used in Injection Molding
Several thermoplastics are commonly used in injection molding. Each material has unique properties suited to specific applications.
Here’s a quick overview:
- ABS: Known for its high rigidity and impact resistance, ABS is widely used in automotive parts, consumer electronics, and toys.
- Polypropylene (PP): This material offers excellent fatigue resistance, making it ideal for products like living hinges, containers, and automotive components.
- Polycarbonate (PC): With its high impact strength and optical clarity, polycarbonate is often used in the production of eyewear lenses, medical devices, and protective gear.
Advantages of the Injection Molding Process
Injection molding offers significant benefits in manufacturing.
First, it’s incredibly efficient for producing large volumes of parts. The process allows for rapid production cycles that are ideal for high-demand industries.
Additionally, injection molding provides precision. The ability to replicate parts with tight tolerances means that each piece is nearly identical.
Finally, it’s scalable. Whether you need a few thousand units or millions, injection molding can handle the volume with consistent quality by fine-tuning process parameters.
Challenges in Injection Molding
Like any manufacturing process, injection molding comes with its challenges.
Material selection is critical; using the wrong material can result in weak or defective parts.
Mold design is another key factor—if the mold isn’t designed correctly, issues like warping or incomplete fills can occur.
Process control is essential to maintain quality.
Challenges include:
- Warping due to uneven cooling.
- Flash caused by insufficient clamp pressure.
- Material wastage and the need for reprocessing.
Wrapping Up: Expert Injection Molding with JDI Plastics
The injection molding process is indispensable in modern manufacturing. It is an efficient and scalable process that offers precision, reliability, and quality.
Understanding each step and addressing potential challenges help various industries plan and refine their supply chain logistics. Small businesses and major enterprises can equally benefit from a well-run injection molding company.
At JDI Plastics, we are committed to delivering top-tier injection molding services. Our expertise and dedication to innovation allow us to consistently meet and exceed our customers' expectations.
When you choose JDI Plastics, you're choosing quality and reliability every time.