Introduction - Revolutionizing the Future
Injection molding is the engine behind the countless gadgets that have reshaped the world - and all of our lives.
Injecting molten plastic into prefabricated molds (literally) shapes the consumer electronics industry. Injection molding products blend durability with design, resulting in endless applications for inventors, manufacturers, and anyone in any industry needing custom-fitted… anything.
This article focuses on injection molding's impact on consumer electronics, from your trusted injection molding company, JDI Plastics.
Key Takeaways
- Injection molding creates essential components for electronics.
- High accuracy in molding allows for efficient large-scale production.
- This manufacturing method reduces expenses, making technology more affordable.
- Eco-friendly manufacturing techniques contribute to environmental sustainability.
- Accelerated development cycles enable faster product launches.
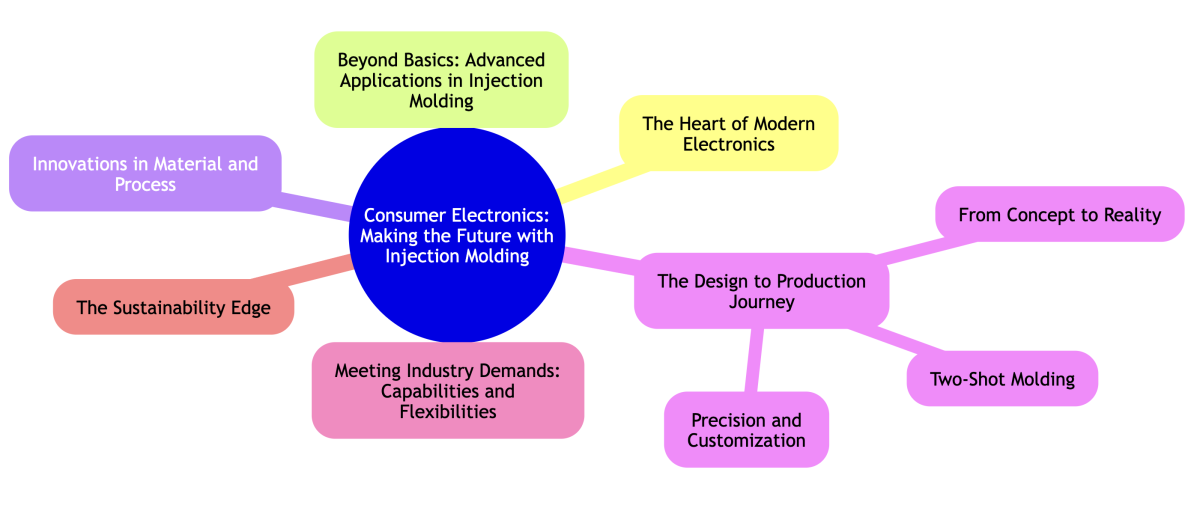
The Heart of Modern Electronics
Injection molding is one of the most significant components of electronics manufacturing. The process breathes life into smartphone components, musical instruments, and more.
Quality products boast highly desired characteristics like durability, aesthetic appeal, and precision functionality.
It's a game-changer, making complex designs and tight tolerances the new norm in the industry.
Beyond Basics: Advanced Applications in Injection Molding
Stepping beyond conventional, injection molding opens doors to innovative applications in electronics.
Crafting precision gears that mesh flawlessly, and designing thermal management components that keep devices cool under pressure - the applications are as vast as the human imagination (or ambition).
- Precision gears for silent, smooth operation.
- Thermal management components for cooler running gadgets.
- Structural electronics that blend form with function.
- Conductive plastics pave the way for future innovations.
- Durable, aesthetic parts enhance device longevity and appeal.
Innovations in Material and Process
The evolution of materials in injection molding has significantly broadened the spectrum of consumer electronics design and functionality.
Recent advancements, especially the integration of two-shot molding, have introduced a level of versatility and efficiency previously unattainable.
This process allows for the combination of different materials in a single component, enhancing both its aesthetic appeal and functional capabilities.
Table 1: Traditional vs. Advanced Injection Molding Materials and Techniques
Feature |
Traditional Injection Molding |
Advanced Injection Molding |
Materials Used |
Standard plastics (e.g., ABS, Polystyrene) |
Engineered resins, composites, conductive polymers |
Manufacturing Flexibility |
Limited by material and mold design |
Enhanced by multi-material, multi-color, and complex designs |
Design Complexity |
Simple to moderate shapes |
Complex geometries with intricate details |
Production Volume |
High volume with longer setup times |
Scalable from low to high volumes with quick setups |
Cost Efficiency |
Economical for large runs, higher waste |
Cost-effective even for small batches, reduced waste |
Sustainability |
Limited use of recycled materials |
Broader use of eco-friendly and recycled materials |
Functionality & Aesthetics |
Functional parts with basic aesthetics. |
Multi-functional parts with superior aesthetics |
Technological Integration |
Conventional molding technologies |
Two-shot molding, over molding, insert molding |
From Concept to Reality
Crafting designs into tangible products relies heavily on advanced engineering techniques and the ability to customize according to specific needs.
The process of turning a concept into a moldable model is intricate, demanding a deep understanding of both the materials involved and the desired outcomes.
Engineering expertise plays a critical role in not only meeting but exceeding expectations.
Two-Shot Molding
Two-shot molding is the new standard of innovation in consumer electronics manufacturing.
This technique produces components with enhanced aesthetics and functionality by molding two different materials in a single cycle. The result is products that offer improved performance, longer lifespan, and appealing designs.
Precision and Customization
Injection molding's capability for high precision and customization accommodates a wide spectrum of manufacturing needs.
Thanks to two-shot molding, manufacturers can bring the most new and complex to life with accuracy and efficiency.
Whether creating custom assembly systems or adapting to specific design requirements, injection molding provides a comprehensive solution for diverse manufacturing challenges.
Meeting Industry Demands: Capabilities and Flexibilities
Injection molding adapts seamlessly to the varied demands of the consumer electronics sector, showcasing remarkable scalability.
Manufacturers can efficiently switch from producing small batches to fulfilling large-scale orders without compromising on the precision or quality of the components.
The method's agility in adjusting to market needs while maintaining high standards is essential in an industry characterized by rapid innovation and evolving consumer preferences.
The Sustainability Edge
Plastic injection molding contributes positively to the sustainability goals of the consumer electronics industry.
Optimizing material use and enabling the incorporation of recycled plastics, reduces waste and promotes circular economy principles.
The process's efficiency and the durability of the produced parts also mean less frequent replacements, further minimizing environmental impact.
Wrapping Up - Crafting the Future, Together.
Injection molding has fundamentally transformed the consumer electronics industry. Its applications are constantly driving innovation and enhancing efficiency.
Through meticulous design and precision manufacturing, this technology has set new standards in product quality and performance.
JDI Plastics is a trusted and experienced injection molding company that offers state-of-the-art products for all industries. With a steadfast commitment to quality and sustainability, JDI Plastics is the ideal partner for shaping the future of consumer electronics.