Minimizing waste in injection molding is a win-win for everybody. It shows a commitment to enhancing operational efficiency and championing sustainability. By adopting these strategies, an injection molding company saves costs and contributes positively to the environment, reducing its carbon footprint and conserving resources.
This guide reveals actionable strategies and best practices to reduce waste across your injection molding operations.
Implementing these measures can significantly boost your company's reputation as a leader in eco-friendly manufacturing, attracting customers who value environmental responsibility.
Key Takeaways
- Precision in scientific molding is crucial.
- Recycling and reusing materials make a difference.
- Lean manufacturing elevates sustainability.
- Waste audits are insightful.
- Training is valuable for refining processes.
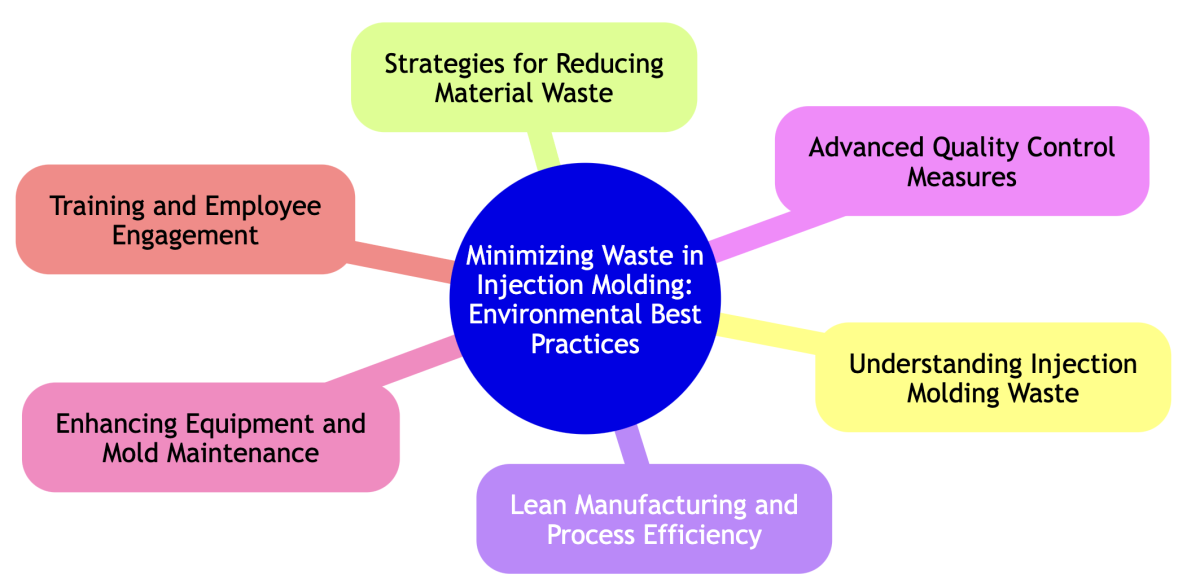
Understanding Injection Molding Waste
Injection molding waste extends beyond scrap material. It represents a multifaceted issue encompassing unnecessary material use, energy wastage, and operational downtime—all of which compromise productivity and sustainability. Identifying these various waste streams is a crucial first step toward implementing greener and more efficient manufacturing processes.
Strategies for Reducing Material Waste
Material waste reduction is significant for environmental and economic health in injection molding. It begins with meticulous material planning to ensure no excess enters the production cycle, extending to adopting recycled and bio-based materials. Here’s a concise roadmap to achieving material efficiency:
Regrind Programs: Implement regrind programs to recycle plastic waste directly into production, reducing raw material costs and environmental impact.
Material Usage Optimization: Employ precise material calculation techniques to minimize excess usage and scrap production, enhancing efficiency.
Use of Recycled Materials: Incorporate high-quality recycled plastics into your manufacturing process to reduce environmental footprint and material costs.
Application of Scientific Molding: Utilize scientific molding to optimize process parameters for reduced waste and improved part quality.
Exploring Bio-based Materials: Invest in bio-based polymers for a greener product line, reducing reliance on fossil fuels and appealing to eco-conscious markets.
Lean Manufacturing and Process Efficiency
Lean manufacturing principles are transformative, focusing on streamlining production, minimizing waste, and enhancing overall efficiency. By scrutinizing every step of the injection molding process, companies can identify non-value-added activities and implement strategies to eliminate them, significantly improving operational performance.
Implementing JIT Inventory Systems
Just-In-Time (JIT) inventory systems are a cornerstone of lean manufacturing, designed to reduce waste associated with overstocking. By synchronizing material orders with production schedules, JIT systems ensure materials arrive precisely when needed, not before. This precision reduces storage costs, frees up warehouse space, and minimizes the risk of material obsolescence. The benefits are clear: lower carrying costs and a more responsive production line.
Continuous Improvement Culture
Cultivating a culture of continuous improvement is essential for sustained efficiency and waste reduction. This approach relies on the collective effort of all employees, from the shop floor to management, to identify inefficiencies and propose solutions.
- Employee Empowerment: Encourage staff to suggest improvements.
- Regular Reviews: Hold frequent meetings to discuss process enhancements.
- Training Programs: Invest in training to enhance skills and knowledge.
- Feedback Loops: Implement systems for feedback to ensure changes are effective.
- Recognition and Rewards: Acknowledge contributions to foster motivation.
Advanced Quality Control Measures
Advanced quality control measures in injection molding are pivotal in minimizing waste and enhancing product quality. Technologies like in-cavity sensors and statistical process control (SPC) provide real-time data on the molding process, allowing for adjustments that prevent defects before they occur. This proactive stance on quality control reduces scrap rates and improves the final products' consistency and reliability.
Effective quality control measures also lower machine downtime. Companies can maintain a continuous production flow by identifying potential issues before they lead to machine stoppages. Moreover, reduced scrap rates mean fewer resources are consumed in producing defective parts, contributing to cost savings and environmental sustainability.
Enhancing Equipment and Mold Maintenance
Regular maintenance is the linchpin of a smoothly running injection molding operation. It prevents unexpected downtime and extends the lifespan of equipment and molds, which are significant investments for any company.
- 1. Regular Inspections: Schedule inspections to catch and fix issues early.
- 2. Proper Lubrication: Follow the manufacturer's guidelines to prevent wear and tear.
- 3. Temperature Control: Ensure systems operate within the optimal temperature range to maintain material properties and mold integrity.
- 4. Component Replacements: Keep an inventory of critical spare parts for quick replacements.
- 5. Cleanliness: Maintain a clean environment to prevent contamination that can lead to defects.
By adhering to these maintenance tips, companies can ensure their injection molding equipment operates efficiently, reducing the risk of costly breakdowns and prolonging the equipment's useful life. This proactive approach to maintenance not only safeguards the investment in the equipment but also supports uninterrupted production, contributing to overall operational efficiency and productivity.
Training and Employee Engagement
Equipping employees with the skills to implement waste reduction strategies and master injection molding techniques is crucial. This sharpens their ability to operate efficiently and instills a proactive approach towards sustainability. Engaged and well-trained teams are the backbone of any successful operation, driving innovation and excellence from within. They spot opportunities for improvement that others might overlook. Let's empower them.
Closing Thoughts
We've covered the essential strategies to curb waste in injection molding operations, spotlighting lean manufacturing, meticulous quality control, diligent equipment maintenance, and the pivotal role of training and engagement. Collectively, these elements forge a path to a more sustainable, productive, and economically sound future in manufacturing. Efficiency and environmental care are intertwined.
JDI Plastics is proud to offer efficient and sustainable injection molding services. Their dedication to excellence and operational efficiency is evident in their products and business practices. Trust JDI Plastics for all your injection molding needs!