Introduction to Automation in Injection Molding
Automation in injection molding has further refined and progressed the manufacturing process by enhancing efficiency and consistency.
Injection molding companies that incorporate automation achieve faster production times, reduced labor costs, and higher quality control. Innovation is a constant mission, and automation leads to more time available for research and development of more efficient processes. This is a positive feedback loop that rewards the motivated pioneers of manufacturing.
JDI Plastics presents this article, shedding light on the benefits of automation in injection molding.
Key Takeaways
- Increased Productivity: Automation speeds up production cycles.
- Improved Precision: Automated systems produce consistent, accurate parts.
- Reduced Labor Costs: Less reliance on manual labor cuts costs.
- Enhanced Safety: Automation minimizes human interaction with machinery.
- Better Quality Control: Continuous monitoring for high standards.
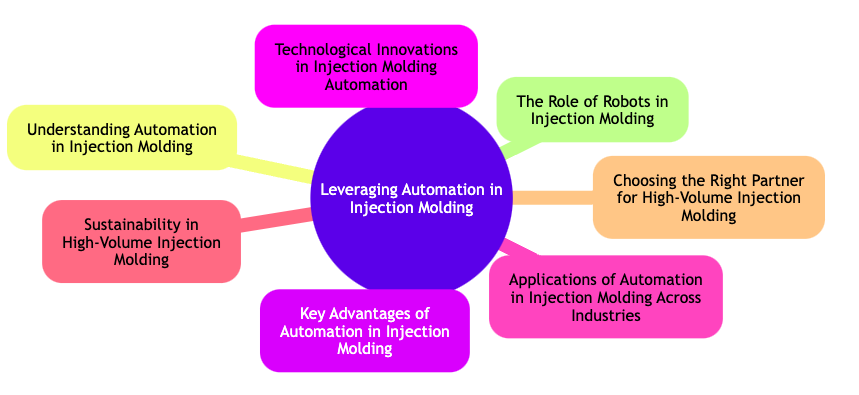
Understanding Automation in Injection Molding
Automation in injection molding replaces manual processes with advanced machinery and robotics.
This shift allows for faster and more accurate production.
While manual injection molding relies on human oversight and labor, automated systems use precision technology to handle tasks more efficiently.
Comparison of Automated and Manual Injection Molding
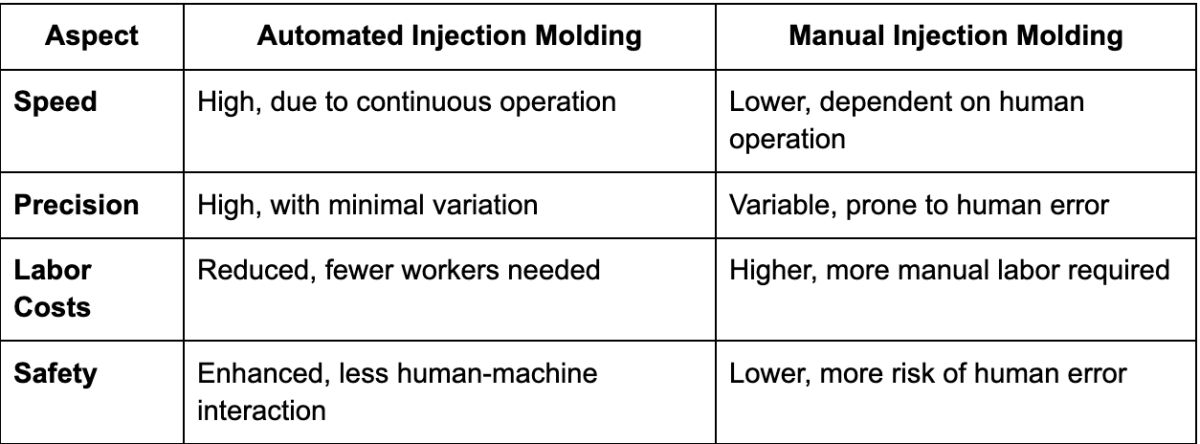
The Role of Robots in Injection Molding
Robots play a crucial role in modern injection molding by performing tasks that require precision and speed.
They handle material feeding, part removal, and assembly with unmatched accuracy.
By integrating robots, manufacturers can achieve seamless operations and maintain consistent quality throughout the production process.
Material Handling and Part Removal
Robots streamline material handling by efficiently feeding raw materials into the injection molding machines.
They also excel in part removal, swiftly extracting molded parts without damaging them. This automated process reduces cycle times and increases overall productivity.
Assembly and Quality Control
In addition to handling and removing parts, robots help assemble components, perfectly fitting each piece.
They also conduct quality control checks, identifying defects and deviations in real-time. This dual role in assembly and inspection guarantees that only high-quality products proceed to the next stage of production.
Key Advantages of Automation in Injection Molding
Increased Productivity
Automation significantly boosts production rates.
Unlike human labor, automated systems operate continuously without the need for breaks. This constant operation reduces cycle times and increases output.
With automation, manufacturers can meet higher demands quickly and efficiently.
Improved Precision
Automated systems deliver exceptional accuracy.
Each part produced is consistent, meeting precise specifications every time. This level of precision minimizes errors and reduces waste, leading to higher quality products and more efficient use of materials.
Reduced Labor Costs
Automation cuts labor costs by reducing the need for manual labor. Automated systems perform tasks that would otherwise require multiple workers. This lowers payroll expenses and reduces the likelihood of human error, further cutting costs associated with rework and waste.
Enhanced Safety
Automation enhances workplace safety by minimizing human interaction with dangerous machinery.
Robots and automated systems handle tasks that could pose risks to workers, such as high-temperature processes and heavy lifting. This shift leads to fewer workplace injuries and a safer working environment.
Better Quality Control
Automation plays a crucial role in maintaining high standards of quality. Automated systems provide real-time monitoring and adjustments, ensuring that each part meets the required specifications.
This continuous oversight helps in early detection of defects and immediate corrective actions, resulting in consistently high-quality products.
Technological Innovations in Injection Molding Automation
Recent technological advancements have transformed injection molding automation, making it more efficient and reliable.
These innovations integrate cutting-edge technology to enhance the entire manufacturing process.
- Real-Time Data Analytics: Provides instant insights for optimizing production.
- IoT Integration: Connects machines for seamless communication and control.
- Advanced Robotics: Enhances precision and speed in material handling and assembly.
- Machine Learning for Predictive Maintenance: Anticipates equipment failures and schedules maintenance.
- Augmented Reality for Training: Uses AR to train employees, improving skill acquisition and safety.
Applications of Automation in Injection Molding Across Industries
Automotive Industry
Automation is essential in producing complex automotive parts with high precision.
It enables the mass production of components like dashboards, bumpers, and engine parts, meeting the stringent quality and safety standards required in the automotive sector.
Medical Devices
Automation is critical for the production of sterile and precise medical components.
Automated systems produce items like syringes, surgical instruments, and implantable devices with the accuracy and cleanliness needed for medical applications, maintaining patient safety and regulatory compliance.
Consumer Electronics
Automation plays a key role in manufacturing small, intricate components in the consumer electronics industry.
Automated systems efficiently produce parts for devices such as smartphones, tablets, and wearable technology, maintaining consistent quality and rapid production to meet market demand.
Packaging
Automation brings efficiency to the production of various packaging solutions.
Automated systems handle tasks such as forming, filling, and sealing packages, maintaining uniformity and speed.
This efficiency is crucial for meeting the high-volume demands of the packaging industry while preserving product integrity.
Sustainability in High-Volume Injection Molding
Focus on Sustainability
JDI Plastics is dedicated to sustainability in their injection molding processes.
We integrate eco-friendly practices to reduce environmental impact while maintaining high production standards.
Our commitment reflects their goal of contributing positively to the environment and meeting the growing demand for sustainable manufacturing solutions.
Eco-Friendly Practices
- Recycled Materials: JDI Plastics is happy to use recycled plastics to significantly reduce waste and conserve valuable resources. This approach supports a circular economy.
- Energy Efficiency: The company invests in energy-efficient machinery, lowering their carbon footprint. These machines use less energy without compromising on production quality.
- Waste Reduction: JDI Plastics optimizes processes to minimize material waste. They implement precise manufacturing techniques that promote recycling within the facility, ensuring efficient material use.
Choosing the Right Partner for High-Volume Injection Molding
Selecting the right injection molding partner is essential for successful high-volume production.
A skilled and experienced partner offers technical expertise, advanced technology, and excellent customer service, resulting in high-quality outcomes.
- Certifications: Look for partners with industry certifications that demonstrate a commitment to quality.
- Technological Capabilities: Advanced machinery and innovative processes are crucial for efficient production.
- Customer Support: A partner known for responsive and helpful customer service is vital for smooth and efficient operations.
Automation in Injection Molding - JDI Plastics
Automation in injection molding significantly enhances efficiency and consistency across various industries. It allows for faster production times, reduced labor costs, and improved quality control, making it an indispensable part of modern manufacturing.
JDI Plastics is a trusted provider of innovative and sustainable injection molding solutions. Our commitment to quality and customer satisfaction means we meet the demands of high-volume production with precision and reliability. You can trust us to source our materials from the highest-quality companies and promote ethical and sustainable practices in every stage of production.
Contact us today to learn more about what we can do for your business!