Introduction to Precision Injection Molding in Microelectronics
Precision injection molding is an increasingly important resource for the microelectronics industry. Its capabilities are incredibly applicable to this industry due to the need for custom-made, tiny parts that meet high-quality standards and precise dimensions.
The demand for defect-free, detailed components is constantly increasing - driving innovation and progress in injection molding.
Injection molding company, JDI Plastics is committed to staying on the cutting edge of these innovations. We uphold the highest standards in our injection molding equipment, materials, training, and early supplier involvement, delivering you a finished product that exceeds expectations. We are everywhere; just google something like "injection molding company Chicago", and we should pop up somewhere!
Key Takeaways
- Improved Accuracy: Precision injection molding achieves high dimensional accuracy.
- Cost-Efficiency: Reduces material waste and manufacturing costs by minimizing defects.
- Material Versatility: Compatible with a wide range of materials, including specialized plastics and composites.
- Enhanced Surface Quality: Produces parts with superior surface finishes, vital for optical and aesthetic applications.
- Reduced Waste: Optimized processes lead to minimal scrap, benefiting both the environment and the bottom line.
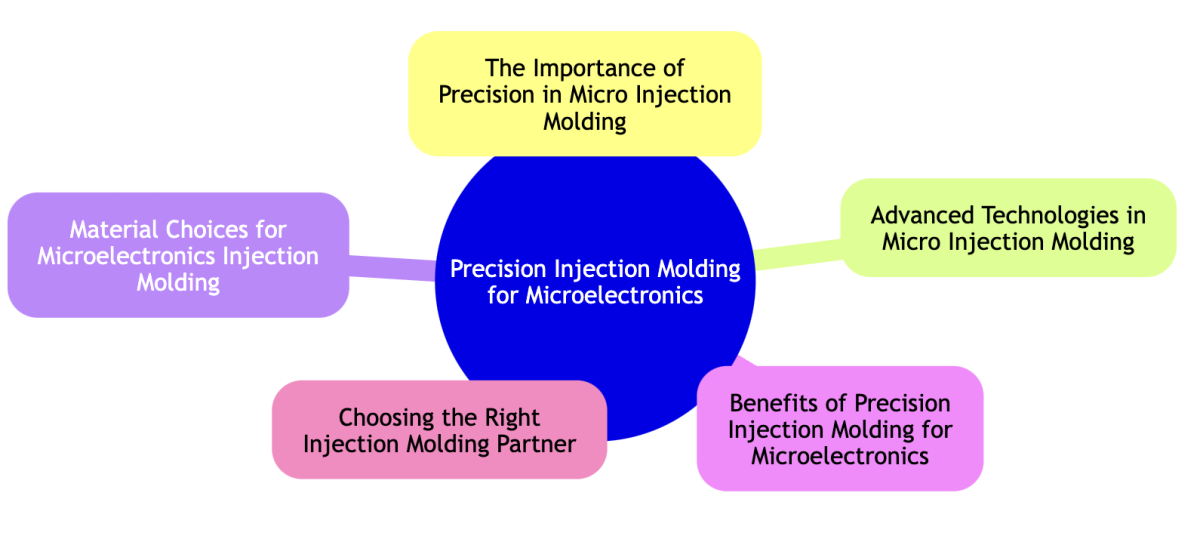
The Importance of Precision in Micro Injection Molding
Precision in micro injection molding is essential for several reasons.
First, it allows for the production of components with minimal defects.
In microelectronics, even the slightest imperfection can lead to product failure. High precision ensures that each part is produced precisely to specifications which reduces the risk of defects that could compromise performance.
Moreover, precision is critical when dealing with complex geometries.
Micro components often have intricate designs that require exact replication. Precision injection molding can consistently produce these complex shapes, maintaining the integrity of the design across large production runs.
This repeatability is key to maintaining quality and performance in microelectronic devices.
Advanced Technologies in Micro Injection Molding
Electric Injection Units
Electric injection units offer high precision and repeatability, essential for producing small parts with tight tolerances.
These units use servo-electric drives that enable precise control over the injection process.
This control maintains consistent quality in micro components. Electric injection units help achieve the necessary accuracy for intricate microelectronic parts by providing exact movements and reducing variability.
Variotherm Processes
Variotherm processes are beneficial for achieving high-gloss surfaces and complete mold cavity filling. These processes involve rapid temperature changes in the mold, which help eliminate weld lines and enhance surface finishes.
By using pressurized water or heat transfer oils, variotherm technology provides detailed accuracy and superior aesthetics in the final product - a technique particularly useful for parts requiring precise surface details.
Digital Assistance Software
Digital assistance software, such as iQ weight control, plays a key role in maintaining consistent part weights.
Software such as this compensates for fluctuations in material viscosity during the injection process and adjusts the injection volume in real time to maintain the accuracy of the final product.
This digital control minimizes scrap and enhances the overall efficiency of the injection molding process, making it ideal for high-precision applications.
Material Choices for Microelectronics Injection Molding
Microelectronics injection molding uses various materials, each selected for its specific properties. Common materials include liquid silicone rubber (LSR) and transparent plastics like PMMA and PC.
- Liquid Silicone Rubber (LSR): Known for its flexibility and heat resistance, LSR is ideal for parts that require durability and consistent performance in varying temperatures.
- PMMA (Acrylic): Offers excellent optical clarity, making it suitable for lenses and other components requiring transparency.
- PC (Polycarbonate): Known for its high impact resistance and strength, PC is used in applications where durability and toughness are needed.
Benefits of Precision Injection Molding for Microelectronics
Precision injection molding offers several advantages for the microelectronics industry.
Firstly, it allows for high-quality surface finishes, which is necessary for components that require clear optical properties or smooth surfaces to function correctly.
The precision of this process ensures that each part meets strict aesthetic and functional standards.
Additionally, precision injection molding minimizes scrap rates. Producing consistent quality parts reduces waste, making the process more cost-effective and environmentally friendly.
Furthermore, this technique excels in efficiently creating complex multi-component parts. By integrating multiple components into a single molding process, manufacturers can reduce assembly time and improve the overall reliability of their products.
Choosing the Right Injection Molding Partner
Selecting the right injection molding partner is critical for success in microelectronics.
Expertise in precision molding and access to advanced technologies is essential. A reliable partner will have the right machinery and a deep understanding of the specific requirements for micro components.
Their experience and capabilities can significantly improve product quality and production efficiency.
- Experience with Micro Components: Look for partners with a proven track record in producing micro parts. Their experience will help avoid common pitfalls and improve outcomes.
- Advanced Machinery: Ensure they have state-of-the-art injection molding machines that can handle the precision and repeatability needed for microelectronics.
- Comprehensive Support Services: A good partner provides extensive support, from initial design to final production. This includes troubleshooting and optimizing the injection molding process.
- Quality Control: Robust quality assurance processes are necessary to maintain high standards and meet stringent industry requirements.
- Flexibility and Scalability: The ability to scale production quickly and adapt to new technologies can give your project a competitive edge.
Final Thoughts - Precision Injection Molding Capabilities
Precision injection molding is an essential component in the microelectronics industry. It meets the stringent requirements for producing small, intricate components with high accuracy.
The benefits of this technology include improved accuracy, cost-efficiency, and the ability to produce high-quality parts with minimal waste. These factors are vital for the success and reliability of microelectronic devices.
JDI Plastics is dedicated to providing top-notch precision injection molding services. Our commitment to quality and innovation makes us a trusted and reliable partner in the microelectronics sector. We serve many industries, including injection molding for packaging, construction, and medical instruments!
We invite you to reach out with questions. Ask about our technology and supplier involvement. We look forward to impressing you!